Quality System
Home » Quality Assurance System
Quality And Production Plan
We make a specific quality control plan for each die casting project, which clearly describes all key product characteristics, and defines inspection methods and standards.
Our engineers issue manufacturing flow charts and work instructions to define how our operators should work accordingly.Process failure mode and effects analysis(FMEA) is performed to ensure defects are prevented during the manufacturing process.
When first sample is ready, we perform full dimension inspection for part qualification, and provide QC datasheet for customer to review.During the production run, we perform SPC control for critical dimensions to monitor and control critical dimension based on 2D drawing.
ISO9001:2015 Quality Management System
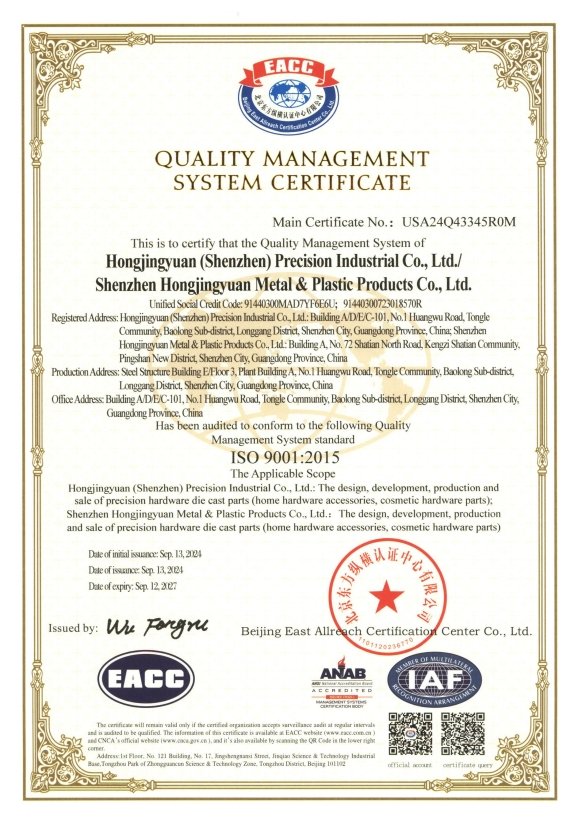
ISO9001:2015
Advantages of Honjenny:
1.As a Chinese factory with 15 production lines, Honjenny focuses on product quality and implements strict quality control processes.
2.The company has passed ISO 9001:2015 certification, which has enhanced the international market competitiveness of its products.
3.In the production process, standardized processes are strictly followed to ensure that every product meets the high quality requirements of customers.
Core principles of ISO 9001:2015:
1.Customer Focus: Understand and meet customer needs and improve customer satisfaction.
2.Leadership: Senior management needs to set clear goals and directions to motivate employees.
3.Engagement of People: Employees are the core of the organization, and their active participation contributes
to the development of the organization.
4.Process Approach: Manage activities and resources as processes to improve efficiency and effectiveness.
5.Continuous Improvement: Organizations should continuously improve their products, services and processes.
6.Evidence-based Decision Making: Decisions should be based on data analysis and information interpretation.
7.Relationship Management: Establish mutually beneficial relationships with suppliers and partners.
The main contents of ISO 9001:2015:
1. Scope: Defines the applicability of the standard.
2. Normative References: Related referenced documents.
3. Terms and Definitions.
4. Context of the Organization: Understand the organization, its environment, and the needs of stakeholders.
5. Leadership: Responsibilities of senior management, quality policy and allocation of responsibilities.
6. Planning: Risks and opportunities, quality objectives and planned changes.
7. Support: Resources, capabilities, awareness, communication and documented information.
8. Operation: Operational control of products and services.
9. Performance Evaluation: Monitoring, measurement, analysis and evaluation.
10. Improvement: Nonconformities and corrective actions, continuous improvement.
Advantages of ISO 9001:2015:
Improve customer satisfaction.
Enhance operational efficiency.
Reduce operational risks.
Enhance the market competitiveness of enterprises.
Enhance employee participation and internal communication.
Gain higher trust in bidding and international markets.
IATF 16949:2016 Quality Management System

IATF 16949:2016
Advantages of Honjenny:
1.As a Chinese factory with 15 production lines, Honjenny focuses on product quality and implements strict quality control processes.
2.The company has passed IATF 16949:2016 certification, which has enhanced the international market competitiveness of its products.
3.In the production process, standardized processes are strictly followed to ensure that every product meets the high quality requirements of customers.
emphasize process-based approaches, focus on risk management and continuous improvement.
require suppliers to apply quality tools in the product and process development stage to ensure product quality and consistency.
emphasize standardization and traceability in the production process, and require verification of special processes.
require the evaluation, selection, monitoring and development of suppliers to ensure the stability of the quality of the supply chain.
encourage organizations to understand and meet the specific needs of automakers.
Require enterprises to develop corrective and preventive measures to prevent problems from recurring.
Encourage enterprises to use data analysis and improvement tools to continuously optimize the quality management system.
IATF 16949 : 2016 Applicable to:
Automotive manufacturers (OEMs)
Tier 1, 2, and 3 suppliers in the automotive industry
Companies that provide automotive parts, service parts, and materials
Benefits of passing IATF 16949 certification:
Enhance the market competitiveness of enterprises
Obtain recognition from international automobile manufacturers
Improve internal management of enterprises and improve production efficiency
Reduce product defect rates and improve customer satisfaction
Promote continuous improvement of enterprises and reduce operational risks
What is APQP?
APQP (Advanced Product Quality Planning) is a systematic approach mainly used for product and process development to ensure that new products can meet customer quality requirements and expectations. It was first developed by the American Automotive Industry Action Group (AIAG) and is widely used in the automotive manufacturing industry and other manufacturing industries.
Main objectives of APQP:
1.Ensure product quality: From design to production, ensure that products always meet customer requirements.
2.Reduce quality risks: Through risk identification and assessment, formulate preventive measures in advance to reduce the occurrence of potential problems.
3.Improve efficiency: optimize development processes, shorten product time to market, and reduce costs.
Five main stages of APQP:
1. Planning and Definition: clarify customer requirements, market needs and project goals, and formulate project plans.
2.Product Design and Development: conduct product design verification, design review, and formulate design control plans.
3.Process Design and Development: formulate production processes, process standards, control plans, and conduct trial runs of production processes.
4.Product and Process Validation: Through small batch trial production, verify whether the product and process are stable, reliable and meet customer requirements.
5.Feedback, Assessment, and Corrective Actions: Continuously monitor the production process, collect feedback, and continuously improve product quality and production efficiency.
Common tools for APQP:
FMEA (Failure Mode and Effect Analysis)
MSA (Measurement System Analysis)
SPC (Statistical Process Control)
PPAP (Production Part Approval Process)
Control Plan
Application scenarios:
In addition to the automotive industry, APQP is also widely used in aerospace, home appliances, electronics, medical devices and other manufacturing industries, especially for projects that require strict quality control and risk management.
If you need more specific APQP implementation methods or applications in specific projects, feel free to let me know!
What is FMEA?
FMEA (Failure Mode and Effects Analysis) is a systematic and forward-looking method for identifying and evaluating potential failure modes and their impact on systems, products or processes, and taking measures to reduce the risk of failure. FMEA is usually used in the quality management of product design (DFMEA), manufacturing process (PFMEA) or service process.
The core steps of FMEA:
1.Identify potential failure modes: Analyze each component of the system, product or process to find possible failure modes (such as component damage, functional failure, process instability, etc.).
2.Analyze the impact of failure: Evaluate the impact of failure modes on the entire system, customers or downstream processes.
3.Determine the cause of failure: Find the root cause of the failure mode (such as material problems, design defects, operational errors).
4.Evaluate risk level: Risk assessment is performed by calculating the risk priority number (RPN), the formula is:
RPN = Severity (S) × Occurrence (O) × Detection (D)RPN = Severity (S) \times Occurrence (O) \times Detection (D)RPN = Severity (S) × Occurrence (O) × Detection (D)
Severity (S): The severity of the failure impact, usually scored 1-10, 10 is the most serious.
Occurrence (O): The possibility of the failure mode occurring, scored 1-10, 10 is the most likely to occur.
Detection (D): The difficulty of the current control measures to detect the failure, scored 1-10, 10 is the most difficult to detect.
5.Formulate improvement measures: For failure modes with high RPN, propose effective improvement measures to reduce risks, including design improvements, process optimization, and additional detection methods.
6.Implement and track improvement effects: implement improvement measures, monitor their effects, and re-evaluate RPN to verify whether the risk is reduced.
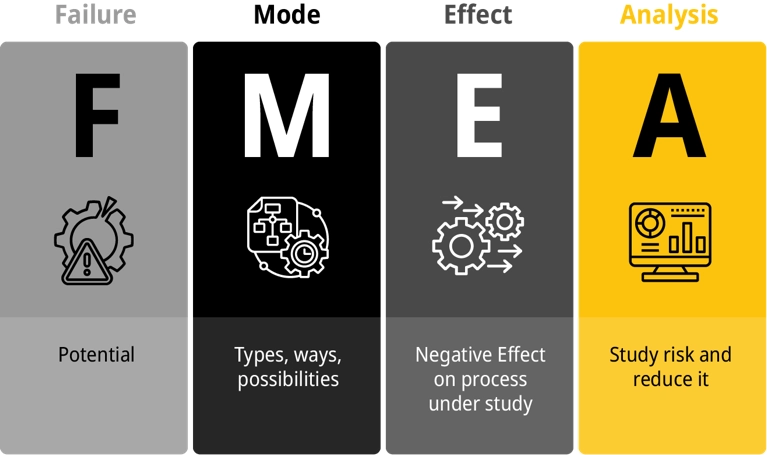
Application scenarios of FMEA:
1.Design stage (DFMEA): In the early stage of product development, optimize product design and improve reliability and safety by evaluating potential risks in the design.
2.Manufacturing process (PFMEA): Used in the production and manufacturing process, improve the stability of the production process and product quality by analyzing potential failure points in the process.
3.Service and system (SFMEA): Applicable to service processes or system operation and maintenance, improve service quality and customer satisfaction by analyzing potential problems in the service process.
Advantages of FMEA:
Identify potential risks in advance and reduce product failure rates.
Standardized risk assessment methods help decision making.
Improve the reliability and safety of products and processes through continuous improvement.
Example:
Suppose that in the process of producing furniture handles, the failure mode of “uneven electroplating” may occur:
Failure mode: Uneven electroplating
Impact: Affects the appearance quality and leads to customer complaints
Cause: Insufficient electroplating time or unstable process parameters
RPN calculation:
Severity (S) = 8 (customers are very concerned about the appearance)
Occurrence (O) = 6 (may occur when process parameters fluctuate)
Detection (D) = 5 (manual inspection is difficult to detect 100%)
RPN = 8 × 6 × 5 = 240
Improvement measures:
Optimize electroplating process parameters and formulate standard operating procedures (SOP)
What is PPAP?
PPAP (Production Part Approval Process) is a quality control method commonly used in the automotive industry and manufacturing industry to ensure that the parts provided by suppliers meet customer requirements and can operate stably and with high quality in actual production. PPAP is usually submitted by suppliers to customers for review and approval before the product is officially mass-produced.
The core purpose of PPAP:
Ensure that suppliers fully understand the customer’s product design requirements.
Ensure that the supplier’s production process is consistent and can continuously produce qualified products.
Ensure that the product operates well in the production environment and there are no potential quality risks.
The main document requirements of PPAP (usually including 18 items):
1.Design Records
2.Engineering Change Documents
3.Customer Engineering Approval
4.Design Failure Mode and Effects Analysis
5.Process Flow Diagram
6.Process Failure Mode and Effects Analysis
7.Control Plan
8.Measurement System Analysis (MSA)
9.Dimensional Results
10.Material / Performance Test Results
11.Initial Process Studies (SPC Statistical Process Control)
12.Qualified Laboratory Documentation
13.Appearance Approval Report (AAR)
14.Sample Product
15.Master Sample
16.Checking Aids
17.Customer Specific Requirements
18.PSW Part Submission Warrant
Five submission levels for PPAP:
Level 1: PSW submission only.
Level 2: PSW and limited samples and supporting data.
Level 3: Complete PPAP submission (most commonly used).
Level 4: Submission method specifically required by customers.
Level 5: Complete PPAP and accept customer on-site audits at any time.
Application scenarios of PPAP:
New product development and production (NPI).
Production process changes (such as changes in equipment, molds, and production locations).
Design changes (product drawings, specification changes).
Changes in raw materials or suppliers.
Revalidation is required after major quality problems occur during the production process.
PPAP was first released by AIAG (Automotive Industry Action Group) and is an important part of IATF 16949 (Automotive Industry Quality Management System Standard) and is widely used in the automotive industry, aerospace, home appliance manufacturing and other fields.
Send Your Inquiry Now
Get Immediate One-On-One Service
Welcome Friends And Customers At Home And Abroad To Cooperate Sincerely And Create Brilliance Together!